圧縮機
砂漠の新都市に、日立の圧縮機を。 国境を越えて巨大プロジェクトを動かす、 エンジニアの挑戦。 砂漠の新都市に、 日立の圧縮機を。 国境を越えて 巨大プロジェクトを動かす、 エンジニアの挑戦。
PROLOGUE
砂漠に囲まれた中東のある国で始まった、新都市開発計画。新たな街のインフラ基盤として、巨大な石油プラントの建設が計画され、その心臓部には、日立製の遠心圧縮機(コンプレッサー)が選ばれた。しかしそれは、日立にとって大きな苦難の始まりでもあった。国家の威信をかけたプロジェクトに、日立が挑む。その舞台裏には、巨大なプロジェクトをゴールへと導いたエンジニアの存在があった。
中東の地で動き出した、日立史上最大の圧縮機プロジェクト。 中東の地で動き出した、 日立史上最大の 圧縮機プロジェクト。
世界の原油埋蔵地、中東。この地域のある国では、石油に依存しない産業構造への転換をめざして、新たな経済都市をつくるという国家プロジェクトが動き出していた。舞台となったのは、海に面した静かな町。プロジェクトはまず、その町の海辺に港湾機能を開発し、と同時に、当面の基幹産業を担う石油プラントと、そのプラントに電力を供給する発電所を建設するところからスタートした。このプロジェクトにおいて中核的な役割を担ったのが、世界的石油会社のX社だ。
X社は、発電所と石油プラントの建設を、数社のプラント建設会社(以下、EPC:Engineering, Procurement, Construction)に発注。このプロジェクトに対して日立は、プラント設備には欠かせない装置である遠心圧縮機を売り込み、X社との関係強化を図りながら、EPC各社に積極的なアプローチを展開した。結果的にすべてのEPCから遠心圧縮機を受注し、同プラントで使用される遠心圧縮機はすべて日立製となることが決定。EPC各社から受注した遠心圧縮機は数十台規模、受注総額は100億円を超え、単独のプラントで使用される圧縮機の受注としては日立における過去最高額となった。
圧縮機とは、プラント設備の心臓部に例えられる装置で、ガスなどの気体を圧縮することによって圧力を高め、その気体の化学反応を促し、プラント設備の隅々に送り届けるための機械。使われるプラントによって種類や機能が違い、1台1台仕様が異なるオーダーメイド品だ。通常、圧縮機を1台製造するのに、受注から出荷まで最短でも13カ月ほどかかる。設計項目も多岐にわたり、特にX社が「プロジェクトスペック」と呼ぶ要求仕様は細部まで厳しい規定があり、1台の圧縮機に対して要求される図面は、なんと約150種類にも及ぶ。図面は1種類で100ページ以上あるものもあり、それらの図面を複数回にわたってやり取りし、修正を重ねていく。日立は、それを数十台受注したのである。ここに、日立史上最大の圧縮機プロジェクトがスタートした。
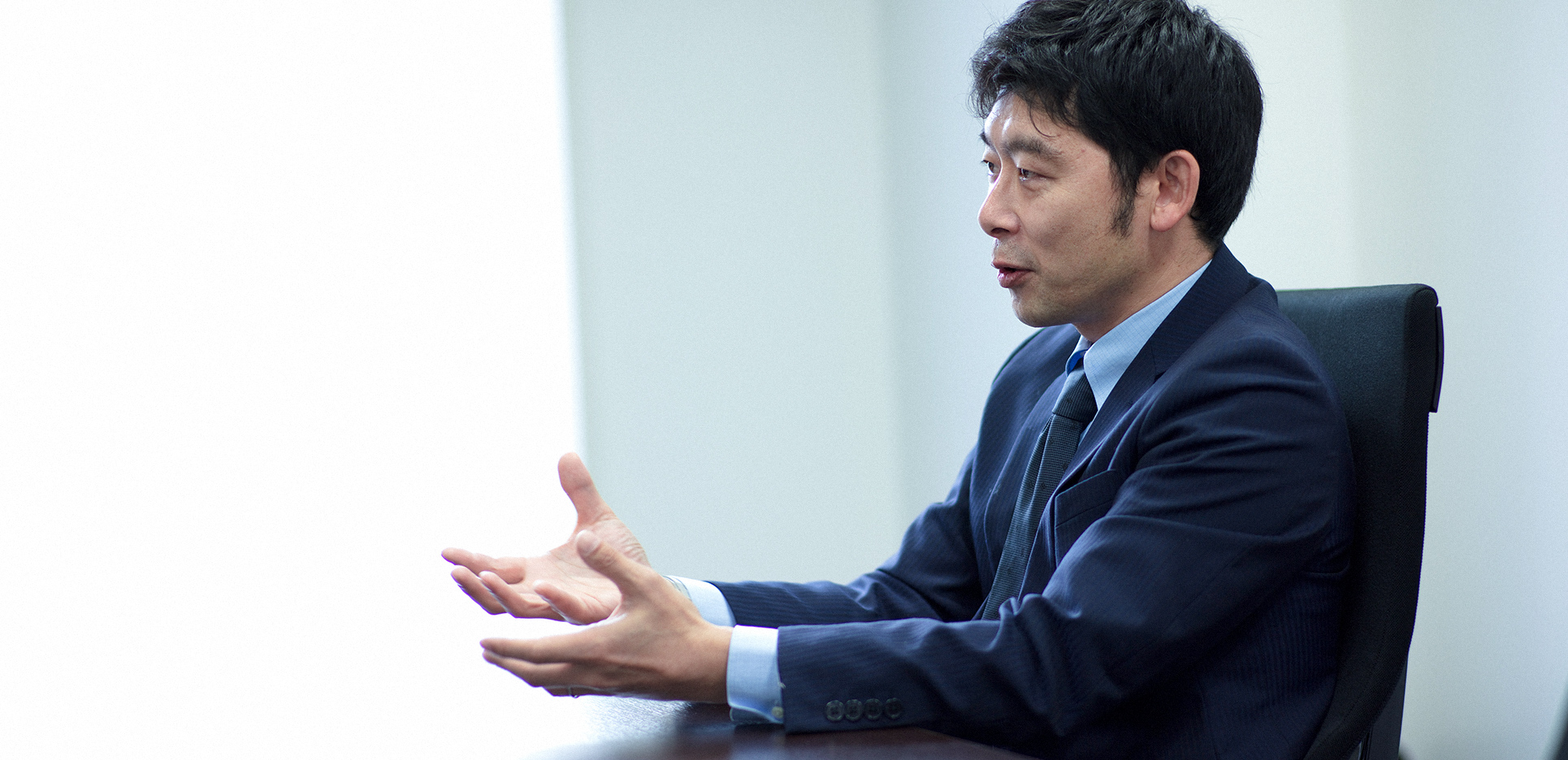
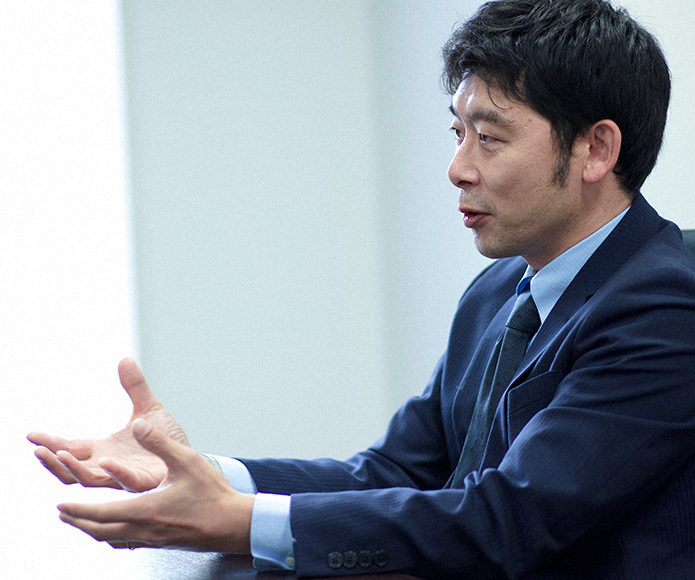
社内外をつなぎ、ケタ違いのプロジェクトを束ねる。 社内外をつなぎ、 ケタ違いの プロジェクトを束ねる。
日立にとっても、100人以上が関わる大プロジェクト。この難事業を、日立側のプロジェクトマネージャーとして統括したのが、フロントエンジニアリング部のマネージャーである長西克幸(以下、長西)と、彼のチームに所属する5名のプロジェクトエンジニアだった。彼らは、社内外をつなぐ「ハブ」となる存在。直接の顧客となるEPCの設計担当者の窓口となり、先方の要望を聞きながら圧縮機の仕様を固め、それを社内の各設計チーム(機械、配管、電気、電気計装など)に伝える。また、圧縮機は、部品の約6割を社外からの調達品が占めるため、ベアリングやドライガスシールといったそれらの部品を仕入れる調達部との連携も求められる。さらに、納入するのは圧縮機単体ではなく、圧縮機を動かすための駆動機(モータ)や制御関連の補機などを合わせたシステムとして納めるため、そうした周辺機械を製造するサブベンダーと呼ばれるメーカーとの図面のやり取りも発生する。そのやり取りが、EPC各社に対し、数十台分あるのだ。「ハブ」とは言っても、じっと待っていられるはずもなく、長西のチームは手分けをして、国内のEPCはもちろん、各国のEPCや中東、そして国内外のサブベンダーの元へと飛び回った。
また、仕様や設計の検討と並行して、製造現場の確保もしなければならない。通常、日立の圧縮機は茨城県の土浦事業所(以下、土浦)で作られていたが、このプロジェクトは受注台数が多く、土浦では製作できないサイズのオーダーもあったため、茨城県の国分事業所、鹿島事業所と、山口県の笠戸事業所にも協力を仰ぎ、土浦とあわせて4カ所の工場で製作することになった。
当時の状況を振り返って、長西は言う。「通常の案件なら、EPCは1社、工場は土浦のみですが、このプロジェクトはまさにケタ違い。これまで多くのプロジェクトを取りまとめてきましたが、スペック、分量、期間、どれをとっても過去最難関と言えるプロジェクトでしたね」。
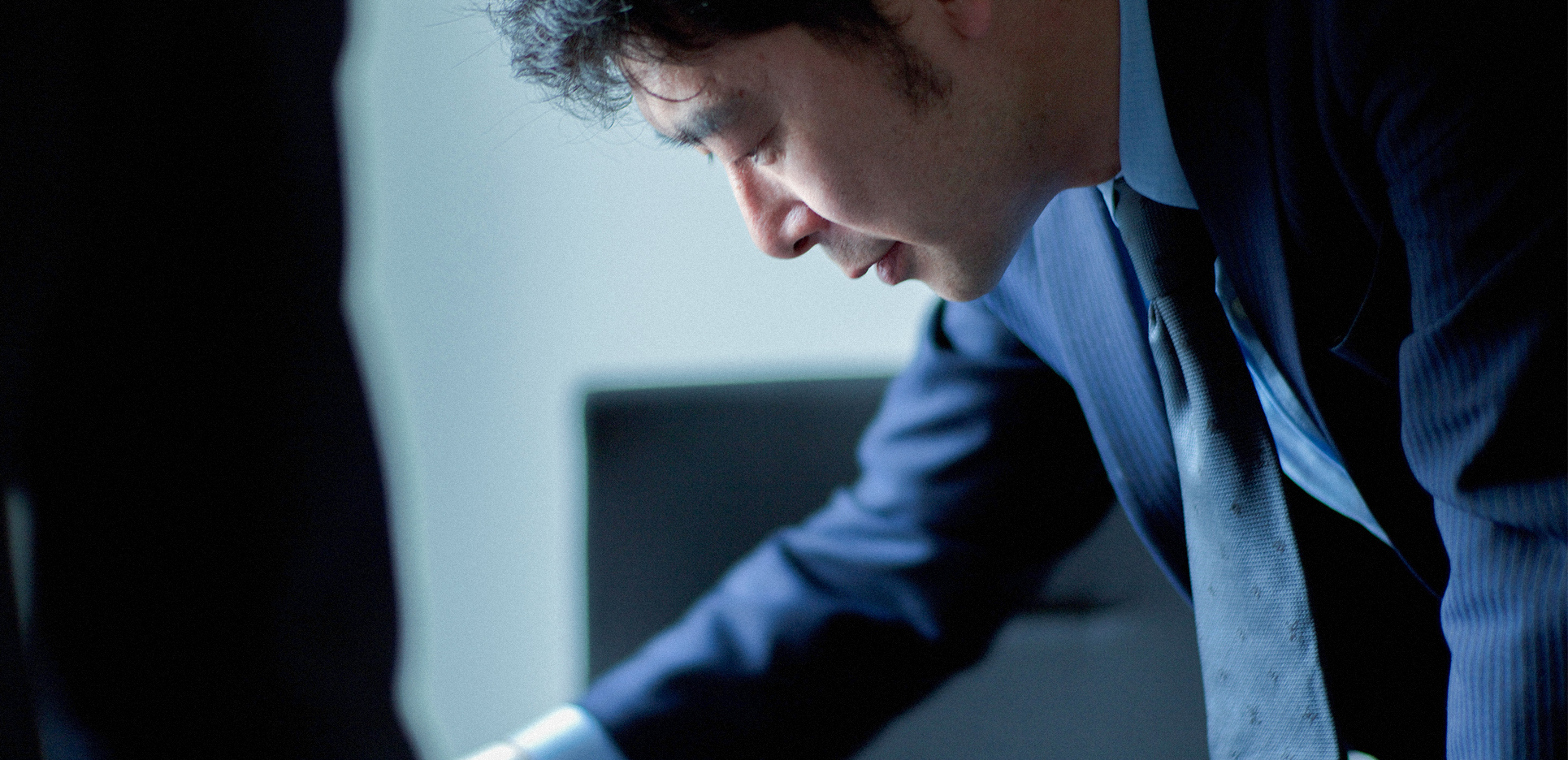
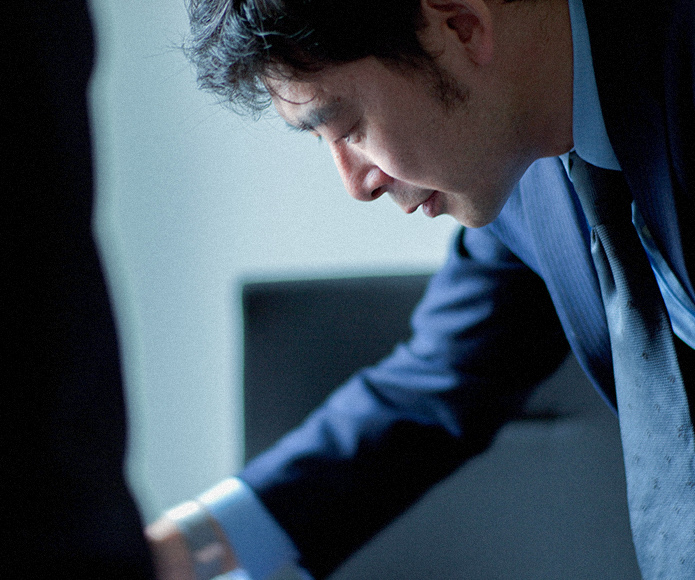
国境も、企業文化のちがいも、乗り越える。 国境も、 企業文化のちがいも、 乗り越える。
長西が特に苦心したのは、EPC各社の考え方の違いだった。国籍も会社規模も文化的な背景も異なる会社では、同じ圧縮機に対しても、要求することや技術的な解釈が大きく異なる。例えば、スペックひとつ取っても捉え方が変わる。A社は、契約にとても厳格で、顧客であるX社の要求スペックを忠実に順守し、一つひとつX社に確認を取りながら進めていく。B社は、柔軟に契約を解釈し、「きっと大丈夫だ、先に進めてくれ」と言ってくる。長西が「本当に大丈夫ですか?同じ注文でも、A社はこんな機能をつけていますよ?」と聞いても、「そんなことをして時間もコストもかけるくらいなら、その機能はいらない」と言う。さらにC社は、細かい部分をあまり気にせず「日立に任せる」というスタンス。どのEPCも、同じX社の厳しい基準に従っているにも関わらず、取り組み方にバラつきがあり、それが仕様にも現れてくるのだ。
その違いを、長西が、自動車を例にとってこう説明する。
「例えば、クルマの窓を例にとって説明すると、X社の要求が、窓を開け閉めできること、だとします。それが最低限確保すべき基本性能です。それに対してA社は、電動で開閉できるパワーウインドウを付けようとする。しかしB社は、窓が開け閉めできればいいのだろ?と言って、手動式の窓で進めようとするわけです。確かに、窓を開け閉めできるという基本性能は同じです。しかし、最終的にX社のプラントに日立製の圧縮機が並んだときに、ある個体はパワーウインドウなのに、別の個体は手動式、のようになってしまう。X社からすれば、日立の圧縮機は品質がバラバラじゃないか、と思われてしまうわけです。操作するオペレーターの混乱や操作ミスにもつながりかねません」。
このような状況を避けるために、長西が心掛けたのが「設計思想の統一を図り、そこからブレない」こと。ある1社のEPCのスペック解釈にあわせて仕様を変更してしまうと、残りのEPCの圧縮機と仕様面での差が出てしまう。そのような違いが発生しないように、設計段階で各社の足並みを揃え、途中でどこか1社が仕様を変更しようとしても、粘り強く交渉を重ね、できるかぎり仕様が標準化されるようにコントロールした。社内のハブとしてだけでなく、社外のハブにもなって、プロジェクトをマネジメントする。それが、プロジェクトエンジニアの仕事なのだ。
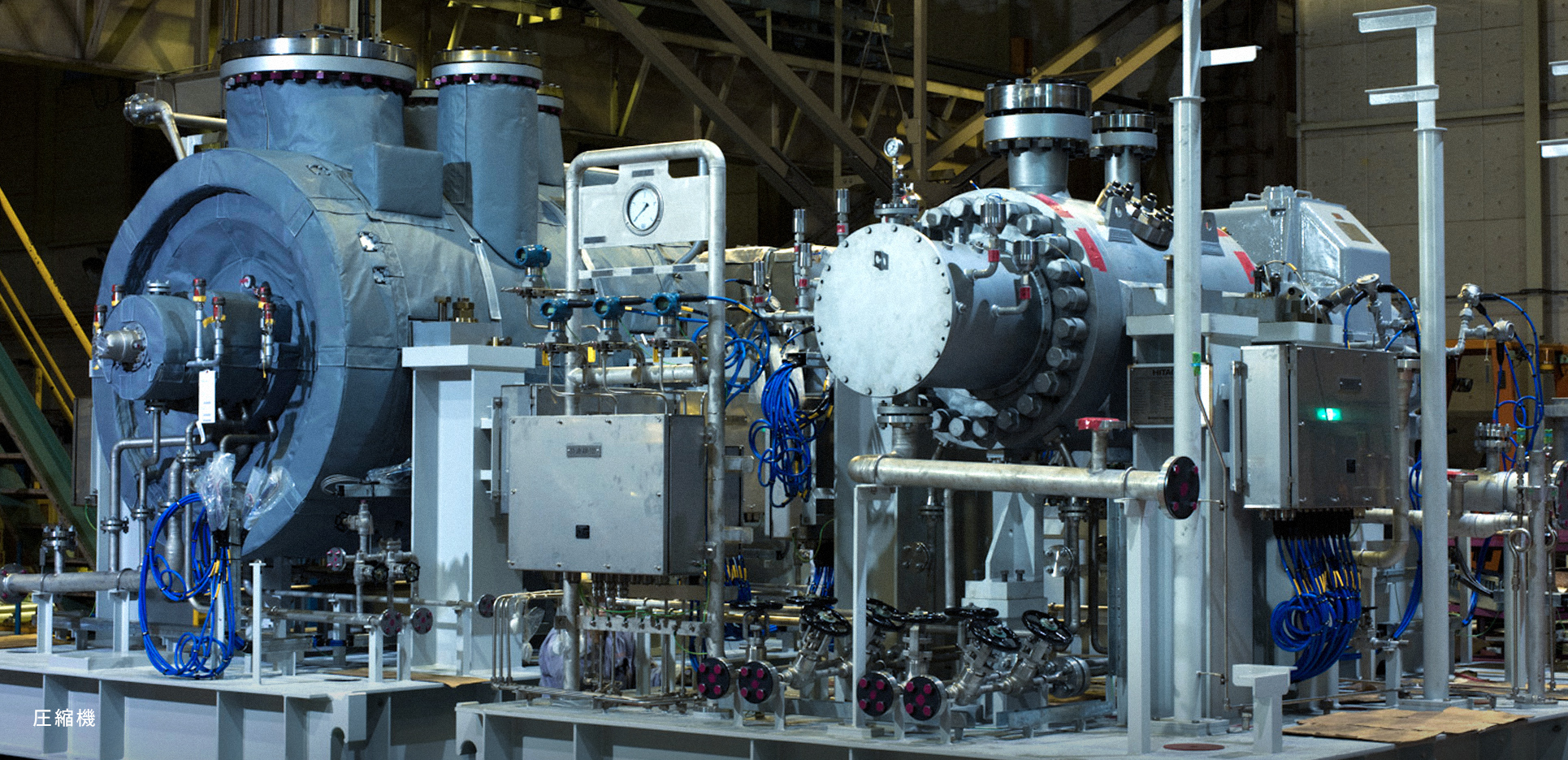
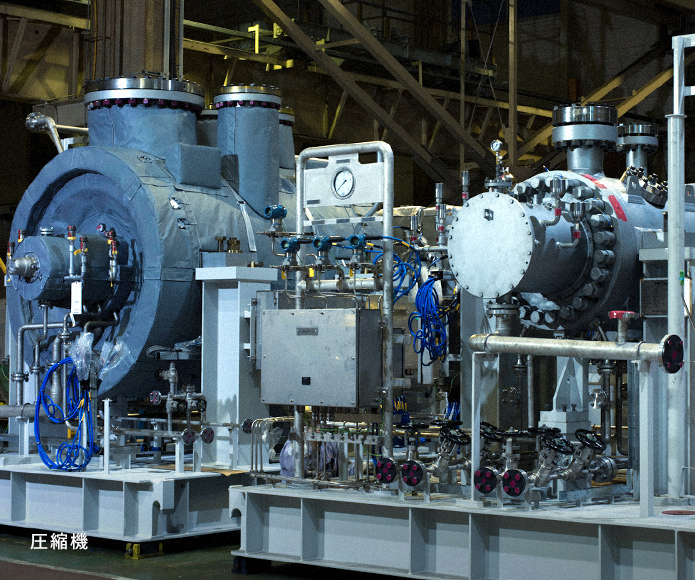
後戻りできない状況で、まさかのトラブル発生。 後戻りできない状況で、 まさかのトラブル発生。
そんなある日、プロジェクトを揺るがす「事件」が起こる。圧縮機システムを構成する重要なユニット装置を請け負っていたあるサブベンダーが、X社の厳しい要求に応えきれず、突然製作を投げ出してしまったのだ。圧縮機はシステム品なので、納期から逆算してすべてのパーツが集まるように工程を組み立てている。それが、ひとつでも来ないとなると、工程すべてが崩れてしまう。予想もしない衝撃の展開。
それでも時計の針は進む。長西は嘆く時間すら惜しむように、代わりのベンダー探しに奔走した。
「このときはさすがに慌てましたね。ようやく仕様が固まって、あとはモノを作るだけという段階でした。代わりの候補となるベンダーに図面を渡しても、相手の理解を待つ時間がない。図面を抱えて押しかけ半分で全国のメーカーに直接説明しに行き、今こういう圧縮機を作っていて、こういう装置が必要で、この納期までにできますか?できませんか?どっちですか!?というような状況でしたね(笑)」
そして、ここでもまたEPC各社の反応が割れる。X社は、そのユニット装置も含めた「圧縮機システム」全体での運転テストを求めていた。当然、本来であれば、その装置をつけた状態でテストを行うべきだが、今はそれが無い状況だ。柔軟なB社は、「その装置はなくても大丈夫だよ。圧縮機単体でテストすればいい」と主張。一方、厳格なA社は、「いや、ダメだ。この装置がなければテストはできない。何としてでも装置を作れ」と、譲らない。しかし、その装置の完成を待ってからテストしていては、圧縮機自体の納期も遅れてしまう。長西は、X社に事情を説明するとともに、EPC各社の説得にあたり、最終的にはその装置抜きでの運転テストにこぎつけた。
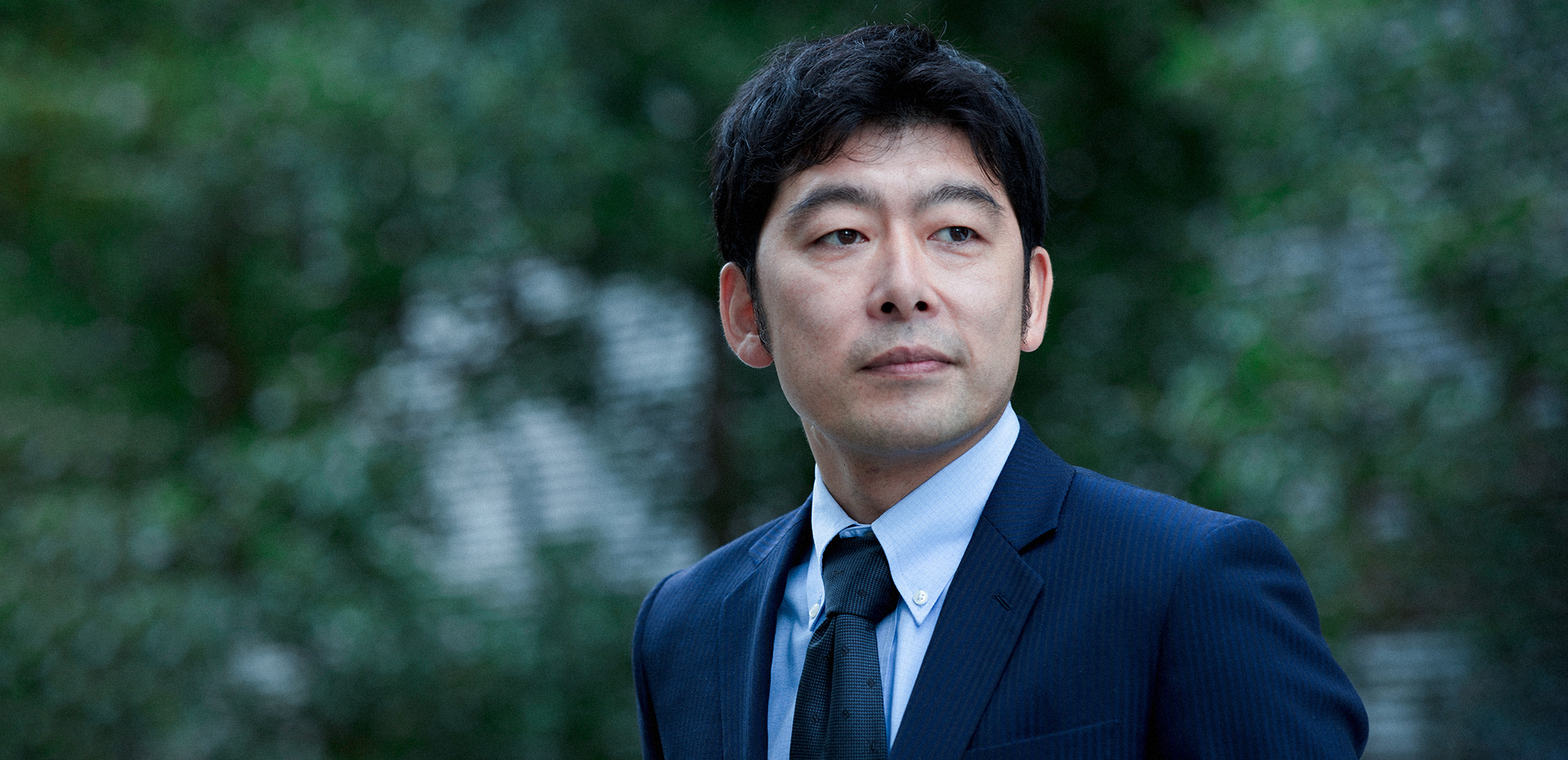
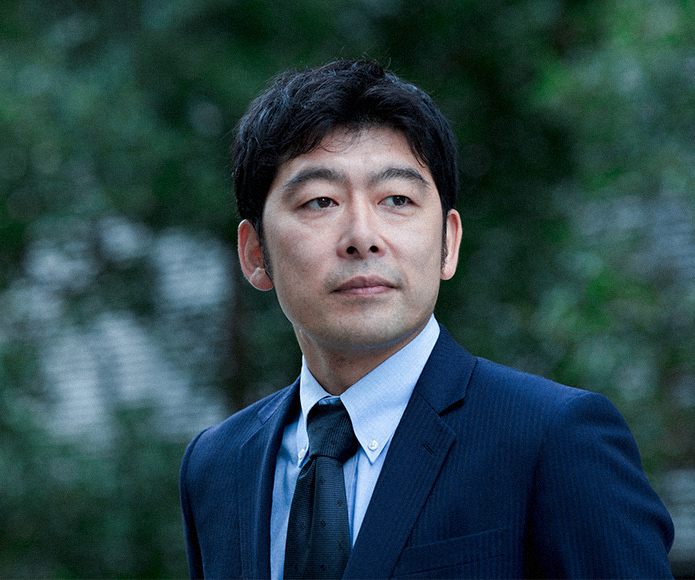
成し遂げたのは、 世界の社会インフラに貢献する仕事。 成し遂げたのは、 世界の社会インフラに 貢献する仕事。
日々、大小さまざまなトラブルが発生する中でも、日立のプロジェクトメンバーの中には途中で脱落する者などいなかった。長西は、どこで何が起きているのか目を配り、大変なときでも誰かが行き詰まったり、チームの雰囲気が暗くなったりしないように心掛けたと言う。何か困っていることがあれば、それを皆で共有し、一緒にトラブルを解決していく。そして、長西自身も、チームのメンバーに支えられたと言う。「当時、私には20年ほどのキャリアがありましたが、それでも毎日必死で、正直、メンバーの深い部分までのケアはできていなかったと思います。しかし、一人ひとりがプロフェッショナルとして主体的に取り組み、彼ら自身でトラブルを解決していってくれた。それが非常に大きな力になったと思います」。
そしてプロジェクト開始から4年、ついにプロジェクトの節目となる製品の出荷を迎えた。このプロジェクトは、日立グループにとって、そして長西個人にとって、どんな意味を持つものだったのか。
「このプロジェクトは、日立にとっての価値も大きかったと思います。一国の経済発展に貢献するプロジェクトであり、世界の社会イノベーション、社会インフラに貢献するという日立の社是にも合致するものです。その意義は非常に大きいと思いますし、日立の名を知らしめるものにもなったと思います。もちろん、私個人のキャリアにとっても、大きなマイルストーンになりました。この先どんなビッグプロジェクトであってもきっと乗り越えられそうな、そんな自信になりました。自分の限界値がだいぶ更新されましたね(笑)」。長西はそう語り、屈託なく笑った。これぞ、日立の仕事。彼の笑顔が、それを物語っていた。
ENGINEER DATA
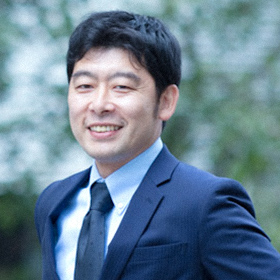
機械システム事業部 気体機システム部 / 1993年入社
機械電気科 卒