ロジスティクスシステム
自律走行ロボットが、 ロジスティクスの未来を救う。 物流倉庫の景色を変えた、 「Racrew」開発プロジェクト。 自律走行ロボットが、 ロジスティクスの未来を 救う。物流倉庫の景色を 変えた、「Racrew」開発 プロジェクト。
PROLOGUE
スマートフォンやパソコンで欲しいものを見つけて購入ボタンを押せば、あっという間に手元に商品が届く。日々進化するeコマース(Electronic Commerce)市場は、私たちの生活にとって欠かせない存在となった。しかし一方で、その生命線とも言える物流の現場では著しい人手不足に陥るなど、大きな課題に直面している。そんな物流業界を変革する救世主として期待されているのが、当社が手がける小型無人搬送ロボット「Racrew(ラックル)」だ。日立グループが数年の歳月をかけて挑んだ開発の裏には、2人のベテランエンジニアによる奮闘があった。
物流業界の課題に、「チーム日立」で挑む。 物流業界の課題に、 「チーム日立」で挑む。
茨城県笠間市。ここに、BtoBのネット通販で急成長を続ける企業の物流拠点がある。東京ドーム2個分の広大な敷地に5,000台を超える棚が並び、1日に対応する配送は数万件。その巨大な倉庫の中を走り回るのが、小型無人搬送ロボット「Racrew」だ。Racrewは、データの指示に従って、倉庫の床に貼られたバーコードを読み取りながら自律走行し、商品が入った棚を持ち上げて指定位置まで運ぶ。この倉庫では、人に代わって154台(2017年導入時)のRacrewが稼働し、物流業務の自動化と省人化、そして生産性の向上に大きな役割を果たしている。
そのRacrewの開発プロジェクトがスタートしたのは2012年。ネット通販による物流量が飛躍的に増え、物流現場での人手不足が顕著になっていたころだった。そのような状況の中でも即日出荷のサービスが定着し、出荷作業にはスピードが求められた。一般的に、作業者が出荷する商品を倉庫内の棚に取りに行くピッキング作業のために歩く時間は、1日の作業時間の半分以上に及ぶと言われ、その効率化は大きな課題となっていた。アメリカでは、物流センターを省人化するための技術が実用化され、日本国内でも、物流現場の技術的なテーマとして、省人化や無人化についての技術が検討され始めた時期。こうした中、産業工場などで使われる「AGV(Automated Guided Vehicle)」と呼ばれる無人搬送車で開発実績があった日立プラントテクノロジー(2013年に日立製作所と吸収合併、現、日立インダストリアルプロダクツ)に、ある物流関連企業から、「AGVの技術を活用してピッキング作業の効率化を図れないか」という相談が寄せられた。
まだ名前すらない自律走行ロボットの計画。その開発を託されたのは、2人のベテランエンジニアだった。主に、車体のハード面の設計を担ったのが、青木邦彦(以下、青木)。そして、車体をどのように動かすか、制御面の設計を担当した、中野浩一(以下、中野)。2人とも長年AGVの開発に関わってきたスペシャリストであり、気心の知れた間柄でもあった。この計画に、日立グループからも心強い仲間が加わった。物流システム全体の研究・技術開発をめざす日立製作所の中央研究所と、ソフトウェア開発会社である日立プラントメカニクス。日立プラントテクノロジーも青木と中野を筆頭に、約20名のメンバーを送り込み、開発体制は整った。
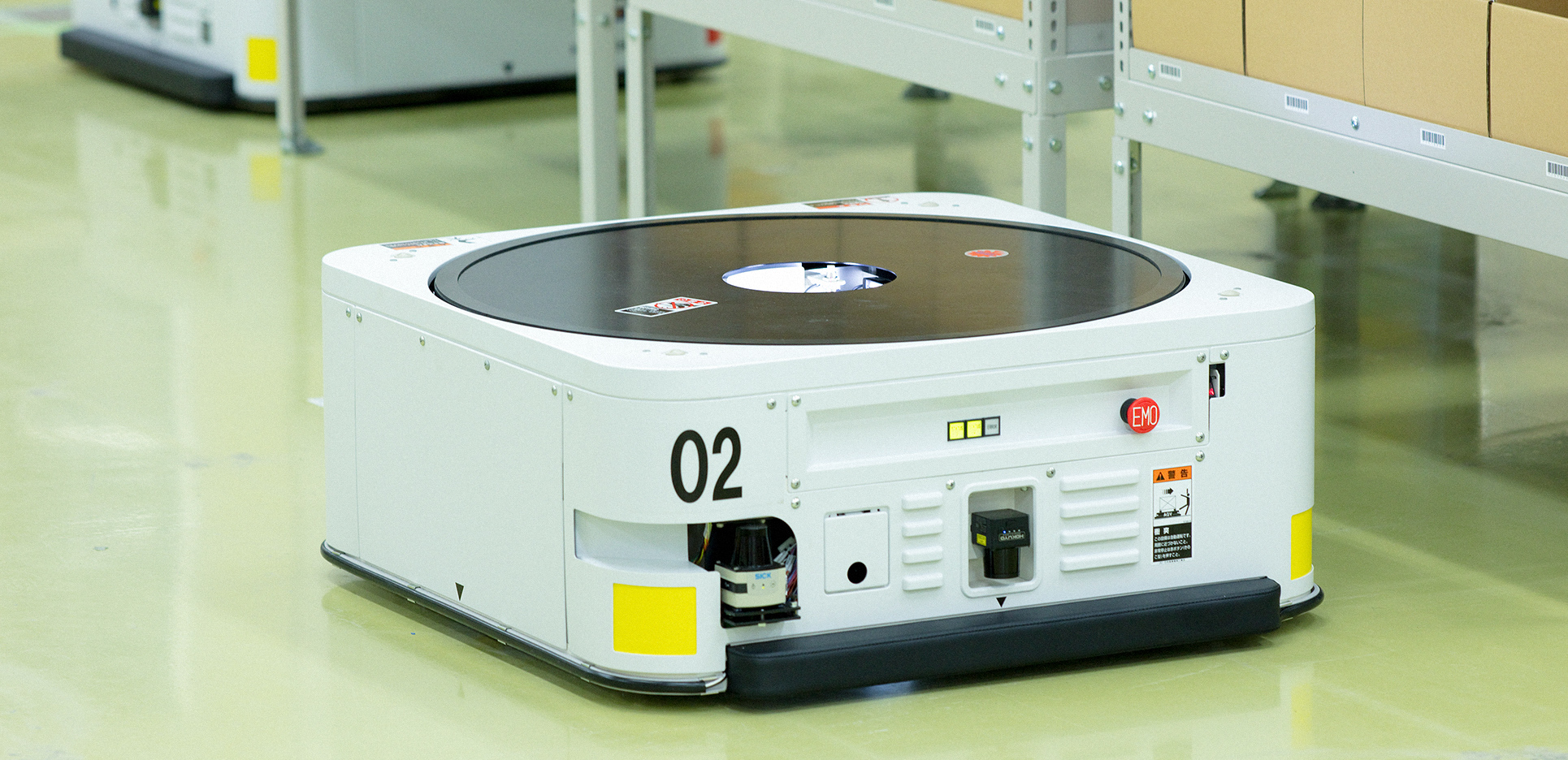
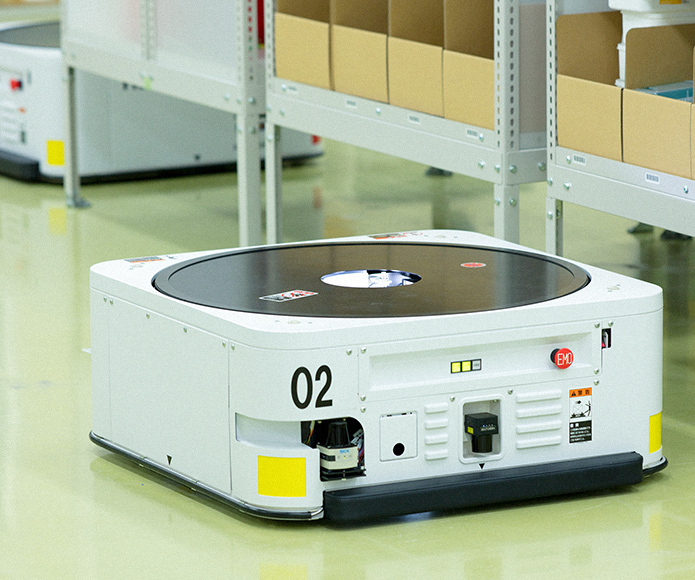
国内初の試みに、次々と現れるいくつもの壁。 国内初の試みに、 次々と現れるいくつもの壁。
Racrewの開発にあたっては、ベンチマークとなるシステムがあった。アメリカのK社が開発したピッキングシステムで、クライアント企業の構想にも近いものだった。しかし、日本国内には前例がなく、競合会社に先行するためにも、開発にはスピードが求められた。そのような中、最初に立ちはだかったのは、K社が築いた特許の壁だった。当然ながら、K社と同じ技術は使えない。開発チームはK社の機械を徹底的に調べ、どのような技術が使われ、どこまでが特許になっているのかを洗い出した。中野は言う。「この調査だけでも、かなり分厚いファイルになりましたね。みんなで手分けしてファイルを読み込んで、相手がこうしているなら、我々はこの方法でやろうとか、K社の特許を避けながら技術的な方針を決めていきました」。
一つひとつ権利関係をクリアにしながら開発が進められる中、ハードの設計を任された青木は、コストの壁にも苦しんでいた。Racrewは、ひとつの物流拠点に対して数十台単位で納入し、運用する構想がベースにある。1台あたりの単価を抑えなければ、システム全体としてのコストが膨れ上がってしまう。「ハード面での設計テーマは、いかに汎用性を持たせるか、ということでした。専用の部品を作るのではなく、市場で手に入る部品で機械を構成するなど、できるだけコストを抑えながら量産できるように考えて、設計をしていきました」。コストとの戦いは、Racrewが完成した今もなお、さらなる改良に向けて続いていると青木は言う。
そして、さらにチームを苦しめたのが制御の壁だった。Racrewが持ち上げる棚の重さは約500kg。その棚を持ち上げながら、少なくとも数十台がお互い干渉することなく、もっとも効率的なルートを選びながら倉庫の中を目標の位置まで自律走行しなければならない。一歩間違えれば、倉庫内でRacrewの事故や大渋滞が起きてしまう。この課題に、チーム日立が一丸となって取り組んだ。採用したのは、倉庫内に碁盤の目状のルートを敷く制御システム。日立製作所の中央研究所が複数のRacrewを運用するための最適なアルゴリズムをはじき出す。それを元に日立プラントメカニクスのチームが制御プログラムを構築する。それを受けて中野がRacrew本体の制御システムを設計し、さらに並行して倉庫内の棚の位置などレイアウトをどうするか、そのレイアウト設計は、青木が中心となって引き受けた。何度もシミュレーションを繰り返し、そのたびにレイアウト設計を見直し、目標とする性能に少しずつ近づいていった。「開発にはいくつもの壁がありましたが、私たちのチーム内には何の壁もありませんでした」。当時を振り返って中野はそう話す。

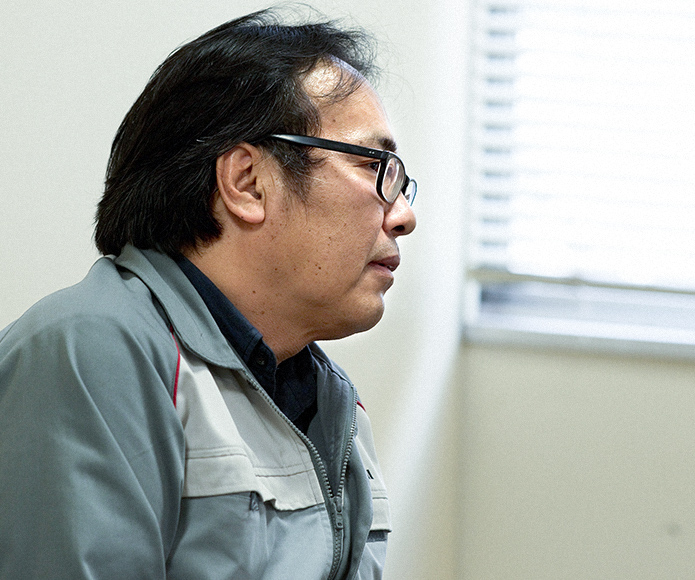
幾多の困難を上回る、モノづくりの喜び。 幾多の困難を上回る、 モノづくりの喜び。
Racrewの完成までには、3台の試作機が作られた。試作1号機は、日立プラントメカニクスが試験的に開発していた車体をベースにしたもの。しかし、スムーズに停止することができないなど、搭載したモータの制御に難があり、加えてコスト面でも課題が残ったため、構成部品の見直しを迫られた。そこでモータの種類を変更。それに伴って本体の設計も見直し、試作2号機が完成した。だが今度は棚を持ち上げる動作がうまくいかず、テーブル部分が傾いてしまうという問題が発生。構造変更を余儀なくされた。開発スピードが要求される中でも、現実はなかなか思い通りには進まない。それでも、チーム内に悲観的な空気はなかった。このころを振り返って、中野は言う。「いきなり問題を解決するようなドラマチックな出来事はありませんでしたが、最初はまっすぐ走らなかったものが少しずつ改善していってまっすぐ走るようになったとか、目標にしていた速度を出せたとか、地道な取り組みが身を結んで、小さな達成感を積み重ねていく。そういう、モノづくりの喜びを感じながらやっていましたね」。
ようやく、理想に近い試作3号機が完成したときには、プロジェクトの開始から約2年の月日が経っていた。そこから、工場内の一角に実際の倉庫に見立てた試験用のピッキングシステムを組み、半年間にわたる試験運用を実施。そして2015年春、晴れて「Racrew初号機」がクライアント企業に納入された。
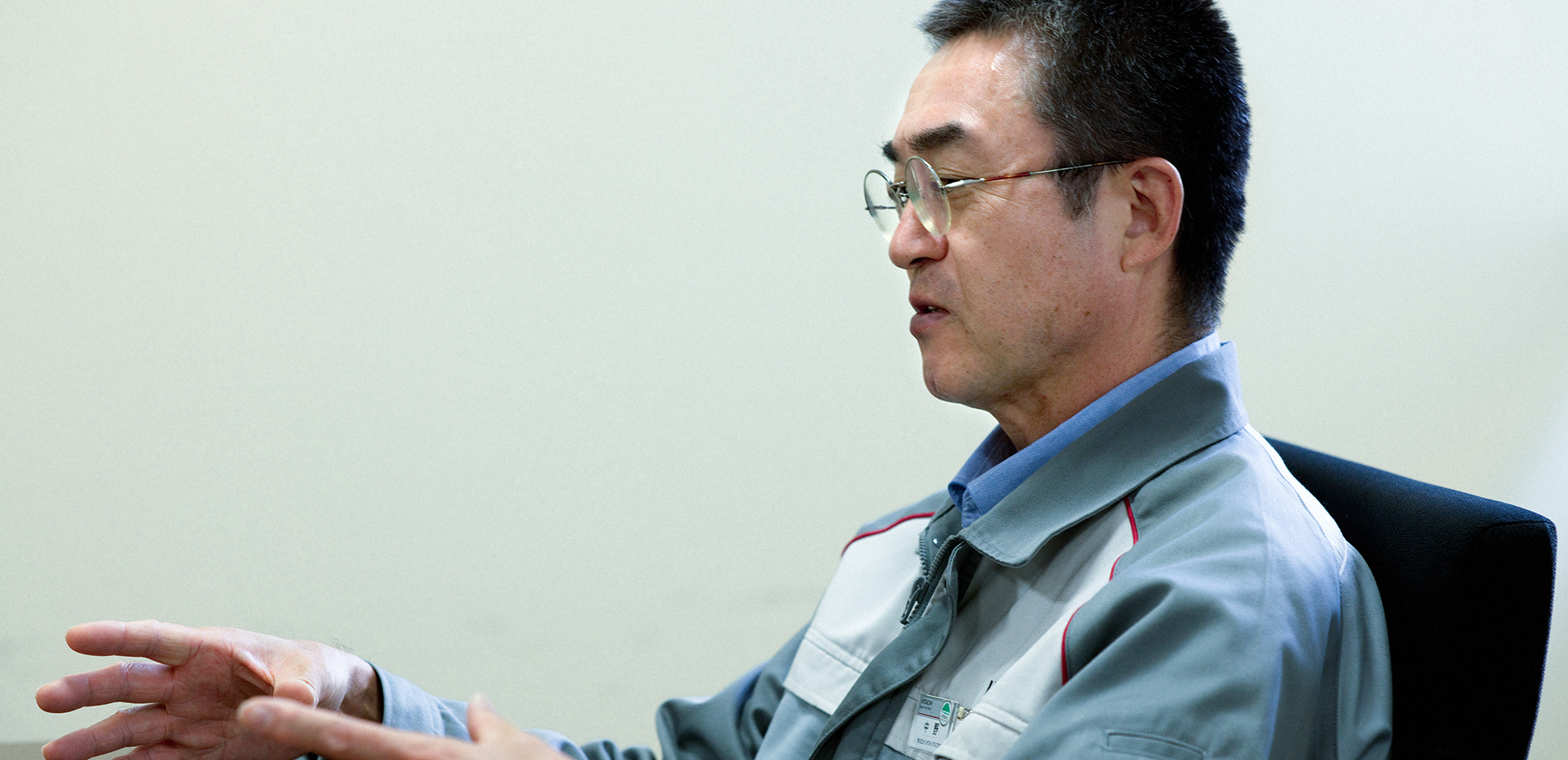
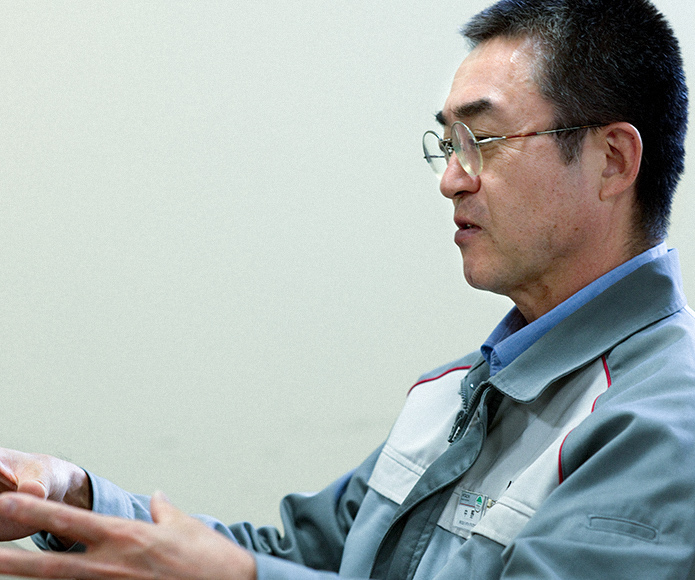
モノづくりの楽しさを、 イノベーションの力に変えていく。 モノづくりの楽しさを、 イノベーションの力に 変えていく。
先述した笠間市の物流センターでは、154台(2017年導入時)のRacrewが稼働している。全てのRacrewを合わせた1日の走行距離は1,300kmに達し、作業者の歩行距離は限りなくゼロになった。ピッキング作業の効率化はもちろん、受注から出荷までの時間が大幅に短縮され、生産性は約2倍になったという。
Racrewを起点にした物流システムの誕生によって、物流倉庫の景色は一変するかもしれない。社会的にも大きな可能性を示したプロジェクト。しかし、今回のプロジェクトを振り返るとき、その中心を担った2人のエンジニアから出た言葉は、自らの成果を誇示するものではなく、モノづくりに対する純粋な思いに満ちた言葉だった。
ハード面の設計を担当した青木は言う。「やっぱり、自分たちがイチから作った製品には愛着があるし、そういう製品が世に出て、広がっていくのは嬉しいですね。やっていてすごく楽しい仕事だったと思います。これからさまざまな技術が発達していくと思いますが、どんな時代になっても、自分の製品に愛着を持てる仕事をするのが大切なのだと思います」。
青木の隣で静かに頷いていた中野が言葉を続ける。「私の場合も、何かを作り上げること自体が面白いと思っています。自分の工夫が製品に直結して、それが実用化されて、社会の役に立つ。そういうモノづくりを、構想の段階からお客さまや仲間と一緒になって作っていくのが楽しいし、働く糧になっていますね」。
今後、Racrewの運用データの取得によって、コンベアなどの周辺設備も含めたロジスティクス全体のイノベーションが加速していくはずだ。さらに、AIやビッグデータを活用すれば、倉庫単体だけではなく、輸送システムも含めたサプライチェーン全体の合理化や最適化にもつながっていく。
そうした近い未来を見つめながら、中野は言った。「Racrewは、駅伝の第1走者のようなものなのです。無人化のための出発点にすぎません。第2走者は、どんなプロダクトが走るのかまだ分かりませんが、いずれにしてもゴールはまだ先にあると思います」。
ゴールはまだ先。これからも2人の挑戦は続いていく。
ENGINEER DATA

機械システム事業部 ロジスティクスシステム部
システム設計グループ / 1986年入社
工学研究科 電気工学専攻 修了
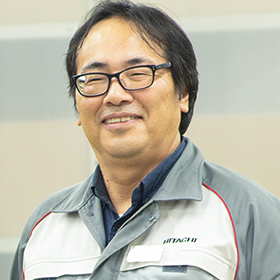
機械システム事業部 ロジスティクスシステム部
システム設計グループ / 1986年入社
機械科 修了